Rex Krueger
Published 13 Sep 2023How to make a hand tool spring pole lathe. Almost.
(more…)
September 14, 2023
I Built a FOOT POWERED Lathe (Most requested video)
September 12, 2023
QotD: The largest input for producing iron in pre-industrial societies
… let’s start with the single largest input for our entire process, measured in either mass or volume – quite literally the largest input resource by an order of magnitude. That’s right, it’s … Trees
The reader may be pardoned for having gotten to this point expecting to begin with exciting furnaces, bellowing roaring flames and melting all and sundry. The thing is, all of that energy has to come from somewhere and that somewhere is, by and large, wood. Now it is absolutely true that there are other common fuels which were probably frequently experimented with and sometimes used, but don’t seem to have been used widely. Manure, used as cooking and heating fuel in many areas of the world where trees were scarce, doesn’t – to my understanding – reach sufficient temperatures for use in iron-working. Peat seems to have similar problems, although my understanding is it can be reduced to charcoal like wood; I haven’t seen any clear evidence this was often done, although one assumes it must have been tried.
Instead, the fuel I gather most people assume was used (to the point that it is what many video-game crafting systems set for) was coal. The problem with coal is that it has to go through a process of coking in order to create a pure mass of carbon (called “coke”) which is suitable for use. Without that conversion, the coal itself both does not burn hot enough, but also is apt to contain lots of sulfur, which will ruin the metal being made with it, as the iron will absorb the sulfur and produce an inferior alloy (sulfur makes the metal brittle, causing it to break rather than bend, and makes it harder to weld too). Indeed, the reason we know that the Romans in Britain experimented with using local coal this way is that analysis of iron produced at Wilderspool, Cheshire during the Roman period revealed the presence of sulfur in the metal which was likely from the coal on the site.
We have records of early experiments with methods of coking coal in Europe beginning in the late 1500s, but the first truly successful effort was that of Abraham Darby in 1709. Prior to that, it seems that the use of coal in iron-production in Europe was minimal (though coal might be used as a fuel for other things like cooking and home heating). In China, development was more rapid and there is evidence that iron-working was being done with coke as early as the eleventh century. But apart from that, by and large the fuel to create all of the heat we’re going to need is going to come from trees.
And, as we’ll see, really quite a lot of trees. Indeed, a staggering number of trees, if iron production is to be done on a major scale. The good news is we needn’t be too picky about what trees we use; ancient writers go on at length about the very specific best woods for ships, spears, shields, or pikes (fir, cornel, poplar or willow, and ash respectively, for the curious), but are far less picky about fuel-woods. Pinewood seems to have been a consistent preference, both Pliny (NH 33.30) and Theophrastus (HP 5.9.1-3) note it as the easiest to use and Buckwald (op cit.) notes its use in medieval Scandinavia as well. But we are also told that chestnut and fir also work well, and we see a fair bit of birch in the archaeological record. So we have our trees, more or less.
Bret Devereaux, “Iron, How Did They Make It? Part II, Trees for Blooms”, A Collection of Unmitigated Pedantry, 2020-09-25.
August 4, 2023
What Does A Smoothing Plane Do? | Paul Sellers
Paul Sellers
Published 7 Apr 2023We live in an age when fewer and fewer people will ever use a hand plane and may never even see one in use. This super-short video shows how and why we woodworkers still use and rely on hand planes today. They are fast and effective and they reduce the need for sandpaper too because the wood comes out super-smooth and level.
(more…)
August 3, 2023
July 27, 2023
“Harvesting” Green Wood from the Side of the Road
Rex Krueger
Published 26 Jul 2023It’s just cutting up wood. Right?
(more…)
April 25, 2023
Planing & Scraping Awkward Grain | Paul Sellers
Paul Sellers
Published 9 Dec 2022I try not to be purposely controversial, but often, the wood demands a completely different tactic when it comes to truing and prepping for further steps like panel making and joinery.
Whereas some will say use this bevel-up or that bevel-down plane, use a York pitch, or whatever, the combination of methods and the addition of a #80 cabinet scraper will get you where you need to be, in very short order, but it might just defy convention.
I show you how to tame some very awkward sycamore in this video.
——————–
(more…)
April 16, 2023
Coopering a 36 gallon beer barrel with hand tools
Jamestown Cooperage
Published 28 Jun 2021I am a practicing traditional cooper who makes barrels, buckets, washtubs, and butter churns by hand. I use mostly traditional skills and handtools to build round, conical wooden vessels for history museums, national parks, and collectors.
February 24, 2023
You may call it “interest cycling”, but I call it “normality”
Tom Knighton on what is apparently called “interest cycling” in hobbies and other leisure-time activities:
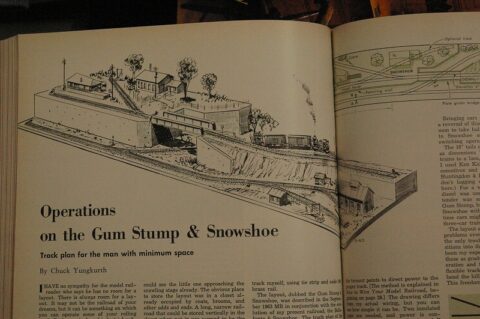
An article from a late 1950s issue of Model Railroader magazine showing a very small HO scale layout plan. The author later admitted that it’s really too small to do much with after it’s built — without some expansion — but the building can take more time than you might expect and you’d need to develop some new skills to do it properly.
Something many ADHD people do — and maybe others, I don’t know — is what I call “interest cycling”.
Basically, I get insanely hyperfocused on one thing, devoting almost all of my time to this One Thing for weeks at a time, then suddenly stop for whatever reason and then jump onto something else.
As a result, I never become truly great at anything. What’s more, since many of these areas of hyperfocus — one article called them obsessions, and with plenty of cause — require money, I end up needing to spend large quantities of money that I really can’t afford to spend.
But, it’s a need.
And it’s a problem. For a lot of us.
See, I have obligations that surround some of my interests. I’m a group leader for the local chapter of an organization I’m part of, for example, that requires not just me to teach a class once per week, but also to advance my own knowledge.
I still teach the class because others are counting on me to do so, but I haven’t been devoting much time to the rest of it, and I should since there are some tangential benefits to what I’m trying to accomplish here at The Knighton Experiment. Sure, some of it isn’t, but that’s just part of the game, so to speak.
What’s worse is that, so far as I’ve been able to find, there aren’t a lot of ways to combat this.
Which suggests that I’m kind of doomed to go through this cycle for the rest of my life.
Now, there are upsides. I mean, there aren’t many people who could detail both how to build a chest of drawers and a 14th-century transitional plate harness, for example. While I can’t necessarily build either with a high degree of proficiency, I at least know what’s involved.
In my own case, those sound like perfectly normal interests — I share both of them — although since my income dropped precipitously several years ago, I don’t spend money as Tom still does. What I have done, however, is to accumulate future stocks of books on those topics I typically cycle through over time so that when the urge strikes I can at least ameliorate some of the need by reading about rather than actively engaging in the hobby/interest/activity. That might be the difference between Tom’s concern and my experience … I cycle among a number of interests, but not brand new ones all the time.
February 16, 2023
Cut the Sliding Dovetail Joint with common hand tools
Rex Krueger
Published 15 Feb 2023There’s another dovetail that you might not know about. Learn to cut it and use it.
(more…)
Twist Solution | Paul Sellers
Paul Sellers
Published 7 Oct 2022Take the guesswork out of truing up a twisted board by setting lines that guarantee dead-on accuracy. When we buy wood, it is often too twisted to work with, so we must remove the twist, cup, and bow.
This quick tip gives you lines to work to with only minimal measuring and a positive outcome.
(more…)
February 9, 2023
Get flat boards EVERY TIME with this simple process // Handtool stock-prep
Rex Krueger
Published 8 Feb 2023Flattening by hand can be intimidating, unless you have a process.
(more…)
February 8, 2023
Hand Planing Awkward Grain | Paul Sellers
Paul Sellers
Published 21 Oct 2022We are often taught to plane in one direction or the other, planing along the grain, but some grain is better planed across the long axis to counter reverse grain caused by the roots of knots in the wood. This goes against the grain with many woodworkers, and yet it can be a perfect solution to get a really good surface.
I am not saying it works every time but more often than you might think; it puts you in the driving seat when wood seems to defy conventional means of planing.
(more…)
January 25, 2023
January 1, 2023
Full Cabin Build – 4K Full Length – Townsends Wilderness Homestead
Townsends
Published 29 Aug 20220:00 – Laying the Foundation
4:39 – The Walls Begin
8:22 – Prepping the Fireplace
9:52 – Finishing the Walls
15:58 – The Roof Design
17:04 – Adding the Purlins
20:29 – The Doorframe
21:32 – The Final Purlins
24:00 – Roofing Materials
25:47 – Adding the Bark Shingles
27:37 – Roof Wrap-Up
29:03 – Door Jams
29:47 – Opening the Fireplace
30:58 – Building the Fireplace
36:06 – Adding the Door
37:54 – The First Fire
39:02 – A Winter Safe Haven
(more…)
November 24, 2022
Can I make an AUTHENTIC Katana from wood?
Rex Krueger
Published 23 Nov 2022Historical weapon, beautiful construction & a great holiday gift, Katanas have it all!
Patrons get all plans early: http://www.patreon.com/rexkrueger
Get the FREE templates!: https://www.rexkrueger.com/store (scroll down to bottom of page).
(more…)